The press section and the drying section are the main components of the paper machine, and its structure and performance are one of the important signs of the paper machine equipment level. The design, production, selection and reasonable configuration of papermaking blankets are conducive to giving full play to the functions of the press section and the drying section and their superior performance, which is the premise of the normal operation of the paper machine and the guarantee of improving the output and quality of the paper. With the rapid development of papermaking technology, the continuous improvement of the level of papermaking equipment, and the emergence of some new grades with high grades and excellent performance, there are more and more varieties of papermaking blankets matching papermaking machines; their performance requirements are also Higher and higher. Therefore, in the selection and maintenance of the types of papermaking blankets, mastering and understanding the types, functions and performances of papermaking blankets as well as their appearance quality and intrinsic quality are particularly important for improving the quality of paper and extending the service life of the blankets.
In the production process of paper, according to the different positions and functions of the blankets used on the paper machine, the papermaking blankets are mainly divided into wet blankets and dry blankets. Generally, the blankets that people call are wet blankets, also known as water blankets, press blankets, etc.
1. Function and performance of wet blanket
1. The role of wet blanket
For the press section of the paper machine, the blanket is one of the important factors that affect the dehydration speed of the press section and improve the performance of the paper sheet. It directly affects the dehydration efficiency of the press section, the internal and external quality of the paper, and the production efficiency of the paper machine This is also the main reason why press felt is one of the valuable consumables.
With the continuous development of papermaking technology and the continuous improvement of the level of papermaking equipment, the matching papermaking blankets have also undergone a long-term development and reform process. At present, as the main part of papermaking felt, the felt for pressing has not only had the functions of dewatering, carrying and conveying, but also has been given more connotation. In combination, it mainly has the following functions.
(1) Absorb the water squeezed from the wet paper web in the nip. The press felt has multiple porosity and water-holding space, and it is easy to transfer the moisture in the wet paper sheet to the felt under the pressure.
(2) Wet paper sheets are supported in the nip to prevent "embossing". In the nip, the press felt pad is attached under the wet paper sheet. The pressure head generated by the moisture in the wet paper sheet under the pressure is evacuated in different directions through the loose porous filter channel of the felt, so as not to make The resulting indenter destroys the formed wet paper sheet and causes embossing or crushing.
(3) In the nip, the stretchability of the felt evenly distributes the pressure on the full-width wet paper sheet. Due to the good elastic recovery of the felt and the loose and porous water filter channel, when the wet paper sheet and the felt enter the pressure zone at the same time, when the pressure is gradually increased, the dewatering pressure potential of the wet paper sheet can be evenly distributed to the felt In order to make the wet paper sheet get a uniform result during the dewatering process of the nip.
(4) Give the paper sheet the desired surface properties. In the press section, the wet paper sheet and the blanket are tightly attached to each other under the pressure. The surface and internal skeleton state of the press felt will directly affect the surface properties of the paper sheet. The rough surface of the felt and the unreasonable structure of the internal skeleton are inevitable. It causes paper diseases such as rough paper surface, large difference between the two sides, heavy base fabric marks, etc. In serious cases, it cannot be alleviated and eliminated in the subsequent process. Therefore, it is very necessary to give the desired surface properties to the paper by choosing a reasonable and high-quality press felt.
(5) In the groove pressure roller, vacuum pressure roller and blind hole pressure roller, there is a difference between the solid part and the eye hole (or groove) on the roller surface, and the blanket can balance the area of the solid part and the eye hole (or groove) ) The pressure on part of the area can eliminate or reduce the hidden marks on the paper. The thick structure of the press felt, incompressible bottom mesh layer, loose and porous water filter channel, good elastic recovery and other properties are the fundamental factors to reduce and eliminate various imprints (hidden) marks.
(6) The wet paper sheet is transferred from the previous press to the next press, which plays the role of transferring the wet paper sheet.
(7) The press felt acts as a power transmission belt, which drives all driven rollers in the press section to rotate.
2. Basic performance of wet blanket
The performance of the blanket we usually mentioned mainly includes three aspects, namely the commonly known "triangle principle", as shown in Figure 1.
(1) Durability
Refers to the durable state of the felt, that is, the life cycle of the felt, and is a comprehensive reflection of all the performance of the papermaking felt. We hope the longer the service life of the paper-making felt is, the better.
(2) Water filtration performance
, Also known as the permeability of the blanket, actually includes the performance of the blanket in terms of water filtration and breathability. This is the most basic performance among the three basic performances of paper blankets. Permeability indicates how easily water or air can penetrate the blanket under a certain pressure or vacuum. In order to meet the requirements of the press, the press felt must have good permeability, otherwise the pressure of the fluid generated in the press nip will be too high and will cause the wet paper sheet to "emboss".
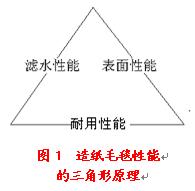
The permeability is related to the structure of the felt, the weaving method and the type and nature of the materials (especially fibers) selected. In addition, the blanket during use must be kept clean, and try to avoid the filler, glue, fine fibers and other external impurities to fill the pores of the blanket, otherwise, the clogging of the blanket pores reduces the permeability of the blanket. In order to give full play to the role of the blanket, the blanket must be continuously washed or periodically cleaned while the paper machine is running, to keep its tissues smooth, permeable, and have a sufficiently large pore volume to fully play the auxiliary dehydration effect of the blanket.
(3) Surface properties
Refers to the thickness and flatness of the surface of the felt. This feature affects the smooth and delicate surface of the wet paper sheet through the pressure of the nip. During pressing, the felt is in direct contact with the wet paper web. Under pressure, the rough or delicate state of the surface of the paper web in contact with the felt is related to the felt. The rough felt surface will form a rough paper surface.
These three properties are the basic performance of papermaking blankets. They are complementary to each other. We must consider them comprehensively when selecting or designing papermaking blankets. We cannot blindly pursue a certain performance and ignore or reduce the other two aspects. performance. The performance of these three aspects of felt can basically meet the general requirements of paper machines.
3. Other properties of wet blanket
With the development of human civilization and the continuous improvement of people's living standards, the requirements for paper quality are getting higher and higher, and the demand for its performance is becoming more and more detailed. In order to meet the requirements of social consumption and reduce the cost of the production process, the width of the paper machine is getting wider and wider, the speed of the vehicle is higher and higher, and the equipment level is also higher and higher. It is getting higher and higher. For this reason, when designing and selecting paper-making blankets, we should not only consider the three performances of the blanket, but should consider all the properties related to the performance of the paper in a comprehensive and balanced way. In this way, the paper-making blanket can be minimized and avoided. Insufficient performance leads to excessive paper diseases and inconvenience in operation. In addition to the above three basic properties of papermaking felts, the following factors must also be taken seriously.
(1) Initial adaptability
Refers to the characteristics of how long it takes to adapt to (or reach) the normal speed of the paper machine and the best state of paper production at the initial stage of the felt loading machine. Different paper-making blankets have different self-performances, and their initial adaptability after machine is also different. Paper workers all hope that the initial adaptation time of the blanket is as short as possible, in order to reduce paper breaks and increase vehicle speed, improve production efficiency and reduce consumption.
(2) High-pressure resistance performance
With the development of paper machine equipment technology, some high-impulse, large roll diameter, wide nip press types are widely used in wide-format high-speed paper machines. The linear pressure of this type of press is particularly high, which requires that the supporting papermaking felt has a high pressure resistance, otherwise it will lose its elasticity and compact in a short time, reducing the water filtration performance. The resistance to high line pressure is related to the structure of the felt. For example, for a bottom net papermaking felt, the more layers of the bottom net, the higher the line pressure resistance.
(3) Elastic recovery performance
Refers to that the papermaking felt is compressed and contracted by the high-line pressure when it enters the nip, and the thickness of the felt recovers after the pressure is eliminated. The better the elastic recovery of the felt in the life cycle, the better the water filtration performance and the longer the service life.
(4) Wear and corrosion resistance
Is a measure of the ability of papermaking blankets to withstand the chemical corrosion of acids and alkalis and the mechanical wear of components in the paper production environment.
(5) Self-cleaning performance
The cleanliness of the papermaking felt during use is directly related to the water filtration performance of the felt itself, and the self-cleaning performance is an indicator to measure the cleanliness of the papermaking felt under the same washing conditions. Papermaking blankets can improve the self-cleaning ability of papermaking blankets by using special raw materials, adjusting their own structural proportions, choosing reasonable layup methods and later chemical treatments.
(6) Compression resistance performance
Is a measure of the ability of the papermaking felt to reduce or eliminate the marks produced by itself and the press roll on the sheet under the action of the nip pressure and vacuum system. Such as the hair marks produced on the surface, the base fabric (base mesh) marks produced by the base fabric (bottom mesh), the groove marks produced by the groove roller, the vacuum marks produced by the vacuum roller, and the blind hole marks produced by the blind hole roller.
(7) Uniform texture performance
The texture of the papermaking blanket is uniform and directly affects the dehydration of the paper sheet and the uniform state of the tissue. This performance is directly related to the uniformity of the web and the bottom net in the production process of the felt, and is closely related to the setting of the washing equipment of the felt and the washing effect.
(8) Breaking strength performance
Press felt should have a certain strength. Periodic stress and fatigue during operation cause the felt to stretch, compress, and strain horizontally. If the blanket is used for too long, the above-mentioned strain reduces the functions that the blanket itself should have and shortens the life of the blanket. It is one of the responsibilities of the papermaking blanket to apply the appropriate tension to make the papermaking blanket tension and overcome all the resistance through the power of the transmission point to drive the components of the press section. The breaking strength performance is a measure of the resistance of the papermaking felt under the high load and tension of the paper machine. The breaking strength of the papermaking felt must be far greater than the tension of the felt during normal production of the paper machine.
(9) void volume performance
The blanket should have a certain water-holding space to absorb the water squeezed from the wet paper in the nip. For blankets of different organizational structures, the water-holding space is different. The larger the water-holding space, the stronger the water carrying capacity of the felt, that is, the better its ability to remove moisture from the wet paper sheet.
All the properties of the above papermaking blankets are very important in the production process of paper. In the selection, design and production of papermaking blankets, these properties and the basic performance of the above three blankets must be considered in a balanced manner. Reduce performance in other areas. as shown in picture 2.
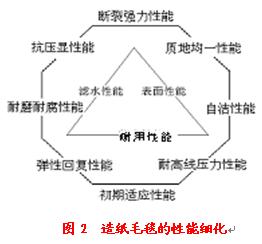
4. Technical parameters for measuring the permeability of wet blankets
Permeability is one of the most basic performances of papermaking blankets. There are four main technical parameters to measure, they are: saturated moisture, vacuum dehydration, air permeability and flow resistance.
(1) Saturated moisture
Saturated moisture refers to the amount of water that can be absorbed per unit weight of the blanket under static conditions. The unit is Kg water per Kg of blanket. Saturated moisture is the best measure of the ability of the felt to receive moisture from the wet paper web in the press zone. The saturated moisture content of the papermaking felt is directly proportional to the water-containing porosity. Table 1 shows the saturated moisture content of common blankets.
(2) Vacuum dehydration amount
Vacuum dehydration refers to the amount of moisture per unit weight of the blanket being sucked out by the vacuum suction box under certain conditions, and its unit is Kg water per Kg blanket. The vacuum dewatering amount of papermaking felt is directly related to factors such as the degree of vacuum, the size of the vacuum opening (hole) area, the air permeability of the felt itself, the dehydration pressure of the vacuum zone, and the hydrophilic performance of the felt fiber raw material. Table 2-1 is the amount of water that can be drawn into the vacuum suction box from various felts when the press device of a test machine is operated at a speed of 457m? Min-1, a slit width of the vacuum suction box of 19mm, and a vacuum degree of 20.3KPa.
(3) Air permeability
The air permeability of the press felt is a key indicator to measure the water filtration performance of the felt itself. Within a certain range, the greater the air permeability of the felt, the better the water filtration performance. The value shown in Table 2-1 is the air permeability of the press felt in the dry state, which is the amount of air (m3) per square meter per minute per square meter under the pressure of 127Pa. The table shows that the new bottom net flocking blanket not only has greater water absorption capacity than the old blanket, but also the water contained in the blanket is easier to be sucked away by the vacuum suction box (roller), and the organizational structure of the blanket is easier to penetrate the air .
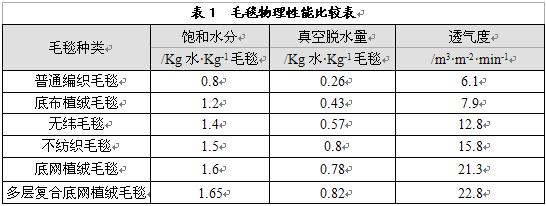
(4) Flow resistance
Flow resistance is another important parameter that affects the dewatering performance of felt. The flow resistance of various felts in a compressed felt, along the longitudinal (L), transverse (X) and vertical directions (Z) of the paper machine, was measured with a water permeability tester specially made by the American Albany International Company . As a result, it is found that the traditional felt has the highest directional resistance, and its value is set to 100 in the test, so that the flow resistance of other wet carpets is based on the base number and expressed as a percentage.
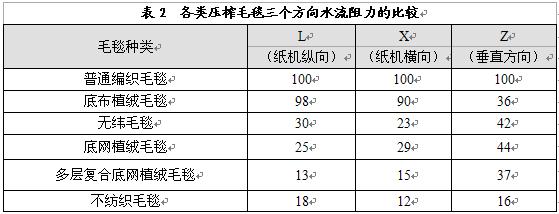
The comparison of the water flow resistance of three kinds of press felts in three directions (measured under a static pressure load of 24.6㎏? Cm-2) is shown in Table 2:
Judging from the comparison results, the latest developed felt performance is the best, that is, the resistance to water flow is small, and it can be easily dehydrated in the felt cleaning and adjusting device. The longitudinal flow resistance of the paper machine in the needle punched felt of the base fabric is almost the same as that of the traditional felt, which is caused by the increase of the resistance when the base fabric is compressed into an oval shape when pressed. The small resistance to water flow may be the main reason for the composite felt to increase the dryness of the paper sheet to 5%. Non-woven blankets (non-base blankets) have the least resistance to water flow.