Dry blankets are used in the dryer section of multi-cylinder paper machines and cardboard machines. They play the role of paper sheet transfer, blanket cylinder drive and foil paper pages to improve heat transfer efficiency and paper flatness. Therefore, the requirements for dry blankets are Good strength, high temperature resistance, smooth surface, good ventilation, stable specifications, etc.
1. Types and characteristics of dry carpet fibers
Since the use of dry carpets, the fibers used in the production of dry carpets include natural fibers such as cotton and asbestos, and synthetic fibers such as polyester fibers, polyamide fibers, polyacrylonitrile fibers, and polyolefin fibers. Early dry carpets used natural fibers, but most dry carpets now use synthetic fibers.
1. Polyester fiber (Polyester)
Is a synthetic fiber composed of terephthalic acid (PTA) and ethylene glycol (EG). The strength, drying resistance, acid resistance, high hydrophobicity and dimensional stability of this fiber are good, so it is used more in the production of dry carpets, but because of the poor steam resistance, the performance has been improving.
2. Polyamide fiber (Polyamide)
Is generally called nylon (Nylon), which has nylon 6 and nylon 6.6 and other points, the performance of the two is basically the same, the difference is that the melting point of nylon 6 is 215 ℃, nylon 6.6 melting point is 255 ℃. This kind of fiber has good abrasion resistance, steaming resistance and strength, but it has poor acid resistance and dimensional stability, so most of them are not used alone but mixed with polyester fiber.
3. Polyacrylonitrile fiber (Polyacrylonitrile)
This fiber is a clothing fiber invented to replace wool. It was used as a raw material for dry carpets in 1960. This kind of fiber has particularly good resistance to steaming heat, and it is quite effective to increase the life of the dry blanket under high temperature and high humidity.
4. Polyolefine fiber (Polyolefine)
This kind of fiber is rich in steaming resistance, corrosion resistance and flex resistance. Generally, the service life of parts with high humidity and high acidity below 130 ℃ is very long.
5. Cotton fiber
Cotton fiber has better water absorption and poorer heat resistance and acid resistance than synthetic fiber. Now it is rarely used again.
6. Other fiber raw materials
In order to make the dry carpet have other properties such as resistance to higher temperature, humidity, antistatic, etc., sometimes some fiber materials such as glass fiber, metal fiber, antistatic fiber, etc. are added to the fiber material.
It should be noted that Nomex (a high temperature resistant nylon fiber) developed by Dupont (DUPONT) is a special nylon fiber with a benzene core. Its characteristics are dry heat resistance and steam heat resistance. The fiber is the best, but because of its high price, it can only be used for the joints, sutures, and base fabrics of dry carpets (nets). Table 1 lists the physical properties of fiber raw materials used in dry carpets for comparison.
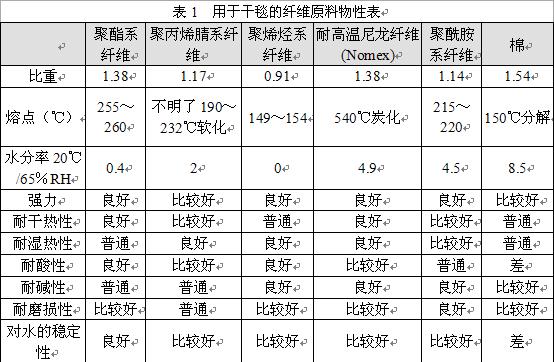
Second, the choice of varieties
Different types of dry blankets are suitable for the drying parts of paper machines and the types of paper that are suitable for production. We should choose according to the different performances of dry blankets. What kind of paper machines and paper types different types of dry blankets are suitable for have been introduced in the content of dry blanket types, which will not be repeated here.
When we choose and use dry carpet varieties, we should pay attention to the following issues:
1. Selection criteria
The requirements for the performance of dryer blankets are different with the types of paper making and working conditions. The criteria for selecting dry blankets are the following two.
(1) Paper quality requirements
According to the requirements of the surface quality of the paper, the selected dry carpet can not cause the surface of the paper to be rough, and must meet the quality requirements of the paper. This is the advantage of the dry carpet.
(2) Drying efficiency standard
Must effectively evaluate the drying efficiency of different drying parts of the paper machine, and select the dry blanket (net) that can adapt to the air permeability according to the evaluation results.
2. The main points of the quality selection of each drying area of the dryer blanket
(1) Wet area
This area is a high-moisture area, which has the greatest impact on the surface of the paper. Special attention should be paid to the surface and joint status of the dry blanket. The paperboard machine that uses waste paper as the raw material to make paper should pay attention to the pollution of the dry blanket (net) When producing high-speed paper machines such as newsprint and cultural paper, attention should be paid to the incitement of paper sheets in dry areas.
(2) Main drying area
This area is the area where water evaporates the most. In order to improve the drying efficiency, a high-permeability dry blanket (mesh) should be used in this area, usually a dry blanket with an air permeability in the range of 1 000 ~ 20 000 cc · min-1 · cm-2 (Net), special attention should be paid to the uniformity of the horizontal moisture of the paper during use.
(3) Rear area (after surface sizing)
Here, a dry blanket (net) that is not easy to adhere to and easy to peel off should be used. Considering the warpage of the paper sheet and the uniform performance of the lateral moisture distribution, a dry blanket (net) with appropriate air permeability should be selected. Is necessary.
3. Selection of dry carpet size
1. Selection of width
The width of the dry blanket should generally be 5 to 10 cm narrower than the width of the dryer surface. If the surface of the cylinder is provided with a paper guide groove, the width of the paper guide groove should be added or removed according to the actual production needs. When choosing the width of the dry blanket, the shrinkage of different dry blankets should also be considered. In general, the shrinkage of ordinary dry blankets is large, generally 6 to 10 cm, and the horizontal direction of BOM dry blankets and flocking dry blanket The shrinkage is relatively small, generally not more than 5cm, especially for dry blankets with a multi-layered base network, the lateral shrinkage is smaller, so the width of the dry blanket should be properly considered.
2. Selection of length
The principle of setting the length of the dry blanket is basically the same as the principle of setting the length of the press felt, that is, the actual detour length when the tensioner is placed at 2/5 ~ 1/2 of the tight direction. When choosing the length of the dry carpet, we must also consider that the different types of dry carpets have different elongation rates. Generally speaking, the ordinary dry carpets have a larger elongation rate of 3% to 5%; The elongation rate is small, generally in the range of 0.6% to 2%, the more the base layer of the dry carpet, the smaller the elongation rate.