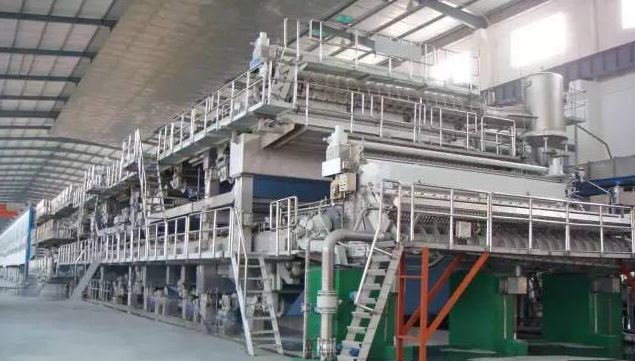
Dehydration mechanism of wet end
A constant function of the forming part, pressing part and drying part of the paper machine is dehydration. In the wet part, mechanical method is often used for dehydration, while in the dry part, evaporation method is used for dehydration. The relative cost of 1 ton of paper is: forming part: pressing part: drying part = 10:12:78; therefore, the paper workers must strive to improve the dehydration efficiency of the wet part, especially the efficiency of the pressing part to reduce the evaporation load of the dry part, and the horizontal dehydration should be uniform.
The dehydration of the paper is the process of curing. A network is formed at the net part. Only the highest vacuum effect is used to make the paper dryness of the couch roll reach 18-23%. Most of the free water in this moisture range has been removed. Further dehydration needs to be completed by pressing to increase the internal water pressure of the paper structure compression. In the process of squeezing, the volume of the paper space is reduced after the moisture in the web is extruded, and a certain degree of fiber compression occurs at the place where the fiber contacts with the fiber. The applied pressure helps to make the moisture distribution in the whole paper even.
The press dehydration is divided into four stages: the press pressure is the sum of water pressure and mechanical pressure, and the wet press area is divided into four stages according to the interaction of water pressure and mechanical pressure.
In the first stage, the air is discharged from the paper and blanket until the paper is saturated and there is no air left. In this stage, the water pressure in the paper is not big and there is no change in dryness.
In the second stage, the paper is saturated with water, and the water pressure in the paper increases, so that the water is transferred from the paper to the blanket. When the blanket is also saturated, the water is discharged from the blanket. In the second stage, it is all the way to the middle of the pressure zone, at this time, the total pressure reaches the maximum.
In the third stage, the pressure gap begins to expand and further dehydrate until the water pressure drops to zero, at this time, the paper dryness is the maximum.
In the fourth stage, the paper and blanket begin to expand, and the paper becomes unsaturated. At this time, with the help of capillary action, vacuum inside the paper or the mechanism of void moisture recovery, some water returns to the paper. The press exit sheet should be separated from the blanket as early as possible to reduce the rewetting effect.
Influencing factors of press dehydration:
① Pressure applied to a unit area;
② Duration of applied pressure;
③ Number of press units;
④ The structure of press roll;
⑤ The characteristics and state of press wool;
⑥ Viscosity (or temperature) of water;
⑦ Paper properties, including the content of fine fiber, dosage and permeability of wet paper.
The main factors to promote dehydration are the water pressure difference of the paper sheet, the residence time of the pressure zone and the uniformity of the pressure. The product of the pressure zone and the residence time is called the pressing impulse; the main resistance is the flow resistance of the paper sheet itself. When the water temperature is increased by 1 ℃, the flow performance is improved by 2.5%. When the temperature of the paper is increased from 20 ℃ to 30 ℃, the dryness of the paper is increased by 2-3%.
There are two types of water removal in press: pressure control type and flow control type. The pressure control type is mainly on the paper with low weight and high freeness. Because the paper is very thin, the paper structure does not obviously restrict the flow of water. The dehydration is mainly determined by the mechanical pressure of the fiber network layer under the pressure of the pressure zone and the possibility of moisture recovery from the blanket to the paper after the middle point of the pressure zone. The flow control type is mainly on the high-volume paper, which is quite thick, and the paper structure restricts the outflow of water from the paper. The paper density, temperature and blanket void ratio have obvious influence on the water resistance, at this time, the residence time in the pressure zone becomes the limiting factor. The pressure control dehydration and flow control dehydration indicate the direction to improve the squeezing efficiency.
Crumple is the direct result of water pressure formed by the lateral movement of water flow in the paper. The method of slow pressurization can avoid the occurrence, improve the structure of the press roller and the selection of blanket, accelerate the dehydration speed, and avoid the occurrence of crushing. There is also a critical point problem in press dehydration. It is uneconomical to press over the critical point for dehydration, or it will compress the paper too much. The water left in the paper should be removed by evaporation. The critical point is 50-57% according to the type of pulp, the form of pressing and the operating conditions.
Papermaking performance of paper machine
The paper making performance of the paper machine refers to the convenient operation and stable performance of the paper machine, which is mainly reflected in the fast and stable transfer of the paper page, with the main purpose of reducing paper break. The transfer of paper web requires the action of force, speed difference traction, vacuum suction and interlining, etc.
In order to improve the operation performance, the following technologies are adopted: vacuum transfer paper introduction, paper transfer vacuum box, paper stabilization air box, paper transfer air box, single hanging dry net, vacuum cylinder, bag area ventilation, automatic tension control, arc roller.
Paper drawing at the couch roll: the paper machine variables that affect wet paper sheet stripping from the couch roll include stripping angle, paper machine speed, relative adhesion of formed paper sheet and forming net. The minimum tension angle is usually between 60 and 120 degrees;
The adhesion to the forming mesh depends on the initial forming conditions, such as mesh concentration, pressure forming degree, mesh cleanliness, etc. There are two types of paper drawing at the couch roll: open type and closed type. The closed type paper drawing can be divided into three types: ordinary roll paper drawing, vacuum roll paper drawing and vacuum paper drawing press. Due to the limitation of wet web strength, the operating speed of the open web is low. When the speed exceeds 7.6m/s, the tension of the speed on the paper page quickly becomes the dominant factor. When the speed reaches 10.2m/s, 60% of the wet web tension in the open web is due to the influence of the speed